The Benefits of Implementing Lean Management Principles
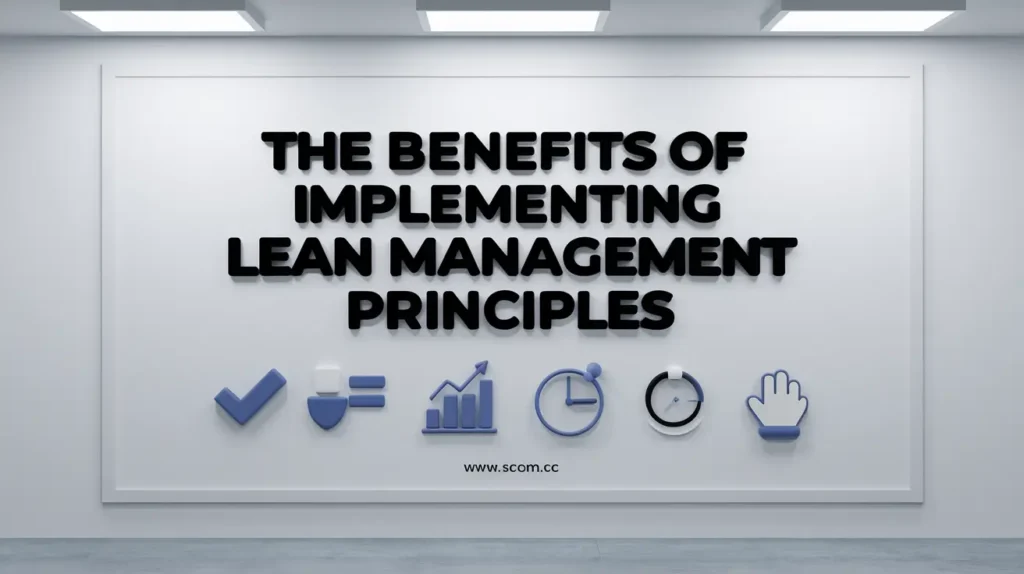
- The Benefits of Implementing Lean Management Principles
- What Are Lean Management Principles?
- How Lean Management Enhances Operational Efficiency
- What Are the Financial Benefits of Lean Management?
- How Lean Management Enhances Quality
- What Are the Benefits of Lean Management for Employee Engagement?
- How Lean Management Can Improve Customer Satisfaction
- What Are the Challenges of Implementing Lean Management?
- How to Sustain Lean Management Practices
- What Are Real-World Examples of Successful Lean Management Implementation?
- How to Get Started with Lean Management in Your Organisation
-
FAQ
- What are lean management principles?
- How does lean management improve operational efficiency?
- What financial benefits can organisations expect from lean management?
- How does lean management enhance product or service quality?
- What are the benefits of lean management for employee engagement?
- What challenges might an organisation face when implementing lean management?
- How can an organisation sustain lean management practices?
The Benefits of Implementing Lean Management Principles
What Are Lean Management Principles?
Lean management principles are methodologies aimed at enhancing value for customers while minimizing waste. Originating from the Japanese manufacturing industry, particularly Toyota, lean management focuses on creating more value with fewer resources. These principles can be applied across various sectors, including manufacturing, services, and healthcare.
Definition of Lean Management
Lean management is a systematic approach to identifying and eliminating waste through continuous improvement, with a focus on optimizing processes to deliver maximum value to customers. The core philosophy revolves around improving efficiency, reducing costs, and increasing quality by streamlining operations.
Key Principles of Lean Management
- Value: Define what value means from the customer's perspective. Value is what the customer is willing to pay for and what meets their needs.
- Value Stream: Map out all the steps in the process to identify value-creating activities and eliminate those that do not add value (waste).
- Flow: Ensure that value-creating steps flow smoothly without interruptions or delays. This involves reducing cycle times and improving process efficiency.
- Pull: Implement a pull system where work is done based on customer demand rather than pushing work through the system based on forecasts.
- Perfection: Strive for continuous improvement by iterating processes to achieve higher efficiency and quality over time.
Examples of Lean Management
- Manufacturing: Toyota Production System, which emphasizes just-in-time production and jidoka (automation with a human touch).
- Healthcare: Lean practices in hospitals to streamline patient flow, reduce wait times, and improve care quality.
How Lean Management Enhances Operational Efficiency
Lean management significantly improves operational efficiency by focusing on eliminating waste, streamlining processes, and optimising resource utilisation.
Ways Lean Management Enhances Efficiency
- Eliminates Waste: Lean principles identify and remove non-value-adding activities, such as excess inventory, overproduction, and unnecessary motion, thereby reducing waste.
- Streamlines Processes: By mapping and analysing processes, lean management identifies bottlenecks and redundancies, leading to more efficient workflows.
- Improves Workflow: Lean techniques, such as 5S (Sort, Set in order, Shine, Standardize, Sustain), help organise workspaces and ensure that tools and materials are easily accessible.
- Reduces Cycle Times: Implementing lean practices can shorten production cycles and lead times by improving process flow and reducing delays.
- Enhances Resource Utilisation: Lean management ensures that resources, including time, labor, and materials, are used effectively and efficiently.
Example of Efficiency Improvement
- Manufacturing: A company reduces its production time by 30% through the implementation of lean principles, such as value stream mapping and cellular manufacturing, resulting in faster delivery and reduced costs.
What Are the Financial Benefits of Lean Management?
Implementing lean management principles can lead to significant financial benefits for organisations, including cost savings, increased profitability, and improved financial performance.
Financial Benefits of Lean Management
- Cost Reduction: Lean practices eliminate wasteful activities and processes, leading to lower operational costs. This includes reduced material waste, lower labor costs, and decreased overhead.
- Increased Profit Margins: By improving efficiency and reducing costs, organisations can enhance their profit margins and overall financial performance.
- Enhanced Return on Investment (ROI): Lean management initiatives often lead to improved ROI by optimising resource use and delivering greater value to customers.
- Reduced Inventory Costs: Lean practices, such as just-in-time inventory, help minimise inventory holding costs and reduce the need for large storage spaces.
- Improved Cash Flow: Efficient processes and reduced cycle times contribute to better cash flow management by accelerating the conversion of inventory into sales revenue.
Example of Financial Improvement
- Retail: A retail company implements lean inventory management and reduces excess stock, leading to a 15% reduction in carrying costs and a 10% increase in cash flow.
How Lean Management Enhances Quality
Lean management not only focuses on efficiency but also plays a crucial role in enhancing quality by improving processes and reducing defects.
Ways Lean Management Enhances Quality
- Focus on Customer Value: Lean management emphasises understanding customer needs and delivering products or services that meet or exceed their expectations.
- Standardisation: Implementing standardised processes and procedures helps maintain consistency and quality in outputs.
- Error Prevention: Lean principles, such as Poka-Yoke (error-proofing), are used to prevent mistakes and defects from occurring in the first place.
- Continuous Improvement: Lean management promotes a culture of continuous improvement (Kaizen), where employees are encouraged to identify and address quality issues proactively.
- Visual Management: Tools like visual controls and performance dashboards help monitor quality and identify problems early in the process.
Example of Quality Improvement
- Healthcare: A hospital implements lean practices to streamline patient care processes, resulting in a significant reduction in medical errors and improved patient outcomes.
What Are the Benefits of Lean Management for Employee Engagement?
Lean management can greatly enhance employee engagement by involving team members in process improvements and creating a more collaborative work environment.
Benefits of Lean Management for Employee Engagement
- Empowerment: Lean management encourages employees to take ownership of their work and contribute ideas for process improvements, leading to greater job satisfaction.
- Collaboration: Lean practices foster a collaborative culture where team members work together to solve problems and achieve common goals.
- Skill Development: Lean management often includes training and development opportunities, helping employees acquire new skills and advance their careers.
- Increased Motivation: Involving employees in decision-making and recognising their contributions can boost motivation and commitment to the organisation.
- Enhanced Communication: Lean practices promote open communication and transparency, improving relationships between employees and management.
Example of Employee Engagement
- Manufacturing: A company introduces lean practices and forms cross-functional teams to tackle process improvements, resulting in increased employee involvement, higher morale, and a 20% reduction in turnover.
How Lean Management Can Improve Customer Satisfaction
Lean management enhances customer satisfaction by focusing on delivering value and improving the quality and efficiency of products or services.
Ways Lean Management Improves Customer Satisfaction
- Faster Delivery: Lean practices, such as reducing cycle times and eliminating delays, lead to faster delivery of products or services, improving customer satisfaction.
- Higher Quality: By emphasising error prevention and continuous improvement, lean management ensures that products or services meet or exceed customer expectations.
- Better Value: Lean management optimises processes to deliver greater value to customers while minimising costs, resulting in more competitive pricing and enhanced value.
- Responsive Service: Lean principles enable organisations to respond more quickly to customer needs and changes in demand, improving service responsiveness.
- Consistent Performance: Standardised processes and visual management tools help maintain consistent performance and reliability, leading to higher customer trust and satisfaction.
Example of Customer Satisfaction Improvement
- Service Industry: A service provider adopts lean practices to streamline its service delivery process, resulting in a 25% reduction in response time and a 15% increase in customer satisfaction scores.
What Are the Challenges of Implementing Lean Management?
While lean management offers numerous benefits, organisations may face challenges during implementation that need to be addressed for successful adoption.
Challenges of Implementing Lean Management
- Resistance to Change: Employees may resist changes to established processes and workflows. Overcoming resistance requires clear communication, training, and involvement of employees in the change process.
- Lack of Leadership Support: Successful lean implementation requires strong leadership support and commitment. Without leadership buy-in, lean initiatives may lack direction and momentum.
- Insufficient Training: Inadequate training can hinder the effective implementation of lean practices. Providing comprehensive training and support is crucial for successful adoption.
- Cultural Barriers: Organisations with entrenched cultures may struggle to embrace lean principles. Cultivating a culture of continuous improvement and collaboration is essential for overcoming these barriers.
- Short-Term Focus: Lean management requires a long-term commitment to continuous improvement. Organisations may face challenges in maintaining focus on long-term goals amidst short-term pressures.
Example of Overcoming Challenges
- Manufacturing: A company faces resistance to lean changes but addresses the issue by involving employees in process improvement teams and providing targeted training, leading to successful lean adoption and improved performance.
How to Sustain Lean Management Practices
Sustaining lean management practices requires ongoing commitment and efforts to maintain and continuously improve lean processes.
Strategies for Sustaining Lean Management Practices
- Continuous Improvement: Foster a culture of continuous improvement (Kaizen) where employees are encouraged to regularly identify and implement process improvements.
- Regular Training: Provide ongoing training and development to ensure that employees stay updated on lean principles and practices.
- Leadership Commitment: Ensure that leadership remains committed to lean practices and actively supports and participates in lean initiatives.
- Performance Measurement: Continuously monitor and measure performance metrics to assess the effectiveness of lean practices and identify areas for improvement.
- Employee Involvement: Involve employees in decision-making and process improvements to maintain engagement and ownership of lean practices.
Example of Sustaining Lean Practices
- Retail: A retail chain establishes a continuous improvement program and implements regular training sessions for employees, ensuring that lean practices are sustained and contribute to ongoing success.
What Are Real-World Examples of Successful Lean Management Implementation?
Examining real-world examples of successful lean management implementation can provide valuable insights and inspiration for organisations seeking to adopt lean principles.
Examples of Successful Lean Management Implementation
- Toyota: Toyotaβs implementation of lean principles, including just-in-time production and continuous improvement, has set a benchmark for lean management in the automotive industry.
- Nike: Nike implemented lean practices in its supply chain to improve efficiency, reduce lead times, and enhance customer satisfaction.
- Boeing: Boeing adopted lean principles in its manufacturing processes to reduce production times and costs, resulting in improved operational efficiency.
- John Deere: John Deere used lean management to streamline its production processes, leading to reduced cycle times and improved product quality.
- Healthcare: The Virginia Mason Medical Center implemented lean practices to improve patient care and reduce wait times, resulting in enhanced patient satisfaction and operational efficiency.
Key Takeaways
- Efficiency Gains: Successful lean implementations lead to significant improvements in efficiency and cost savings.
- Quality Improvement: Lean practices contribute to higher quality products and services by reducing defects and enhancing processes.
- Employee Engagement: Lean management fosters a culture of collaboration and empowerment, leading to higher employee engagement and satisfaction.
How to Get Started with Lean Management in Your Organisation
Getting started with lean management involves a strategic approach to implementing lean principles and practices within your organisation.
Steps to Implement Lean Management
- Assess Current Processes: Evaluate existing processes and identify areas for improvement. Use tools such as value stream mapping to understand current workflows.
- Define Objectives: Set clear objectives for lean implementation, including goals for efficiency, quality, and cost reduction.
- Engage Leadership: Obtain support and commitment from leadership to drive lean initiatives and allocate necessary resources.
- Provide Training: Offer training and education on lean principles and tools to employees at all levels of the organisation.
- Start with Pilot Projects: Begin with pilot projects to test lean practices and refine them before full-scale implementation.
- Monitor and Measure: Track performance metrics and gather feedback to assess the impact of lean practices and make necessary adjustments.
- Scale Up: Expand lean initiatives to other areas of the organisation based on the success of pilot projects and initial results.
Example of Getting Started
- Small Manufacturing Company: A small manufacturing company starts by implementing lean principles in one production line, achieves significant improvements, and gradually expands lean practices to other lines and departments.
Summary Table
Topic | Key Points |
---|---|
Lean Management Principles | Definition, key principles, value, value stream, flow, pull, perfection |
Enhancing Operational Efficiency | Eliminates waste, streamlines processes, improves workflow, reduces cycle times, enhances resource utilisation |
Financial Benefits | Cost reduction, increased profit margins, improved ROI, reduced inventory costs, improved cash flow |
Enhancing Quality | Focus on customer value, standardisation, error prevention, continuous improvement, visual management |
Employee Engagement | Empowerment, collaboration, skill development, motivation, enhanced communication |
Improving Customer Satisfaction | Faster delivery, higher quality, better value, responsive service, consistent performance |
Challenges of Implementation | Resistance to change, lack of leadership support, insufficient training, cultural barriers, short-term focus |
Sustaining Lean Practices | Continuous improvement, regular training, leadership commitment, performance measurement, employee involvement |
Real-World Examples | Toyota, Nike, Boeing, John Deere, Virginia Mason Medical Center |
Getting Started | Assess processes, define objectives, engage leadership, provide training, start with pilot projects, monitor and measure, scale up |
FAQ
What are lean management principles?
Lean management principles focus on creating value for customers while minimizing waste. They include defining value, mapping the value stream, ensuring smooth flow, implementing a pull system, and striving for continuous improvement.
How does lean management improve operational efficiency?
Lean management improves operational efficiency by eliminating waste, streamlining processes, improving workflows, reducing cycle times, and enhancing resource utilisation.
What financial benefits can organisations expect from lean management?
Organisations can expect cost reductions, increased profit margins, improved ROI, reduced inventory costs, and enhanced cash flow from implementing lean management principles.
How does lean management enhance product or service quality?
Lean management enhances quality by focusing on customer value, implementing standardised processes, preventing errors, promoting continuous improvement, and using visual management tools.
What are the benefits of lean management for employee engagement?
Lean management benefits employee engagement by empowering employees, fostering collaboration, providing skill development opportunities, increasing motivation, and enhancing communication.
What challenges might an organisation face when implementing lean management?
Challenges include resistance to change, lack of leadership support, insufficient training, cultural barriers, and maintaining focus amidst short-term pressures.
How can an organisation sustain lean management practices?
Sustain lean practices by fostering a culture of continuous improvement, providing ongoing training, ensuring leadership commitment, monitoring performance, and involving employees in decision-making and process improvements.
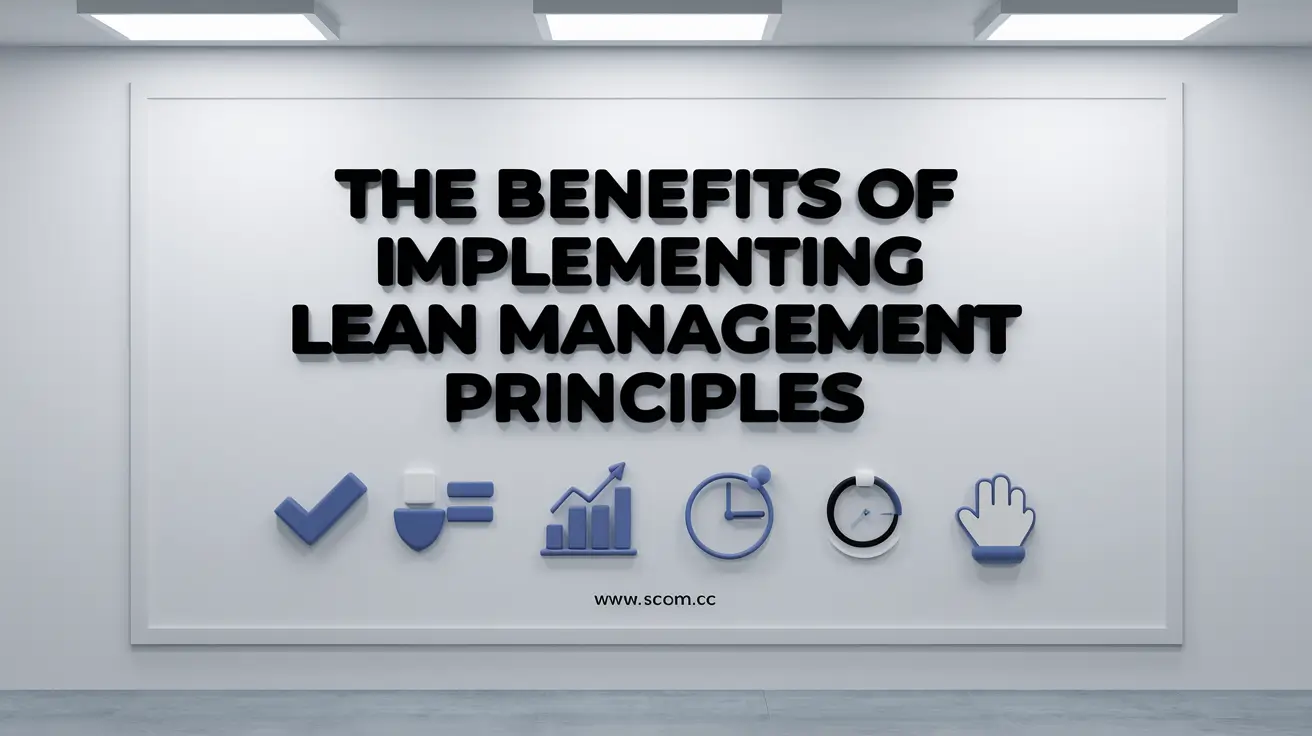
If you enjoyed this article and found it valuable, we encourage you to explore our news and valuable information section, where you'll find more relevant and up-to-date content that may pique your interest. Additionally, if you are seeking advice or need guidance on a specific topic, we suggest visiting our services section. There, you will find a variety of options designed to assist and support you in addressing your needs. Feel free to check out both sections to get the information and assistance that best suits your requirements.
Leave a Reply