How to Streamline Your Business Operations for Better Efficiency
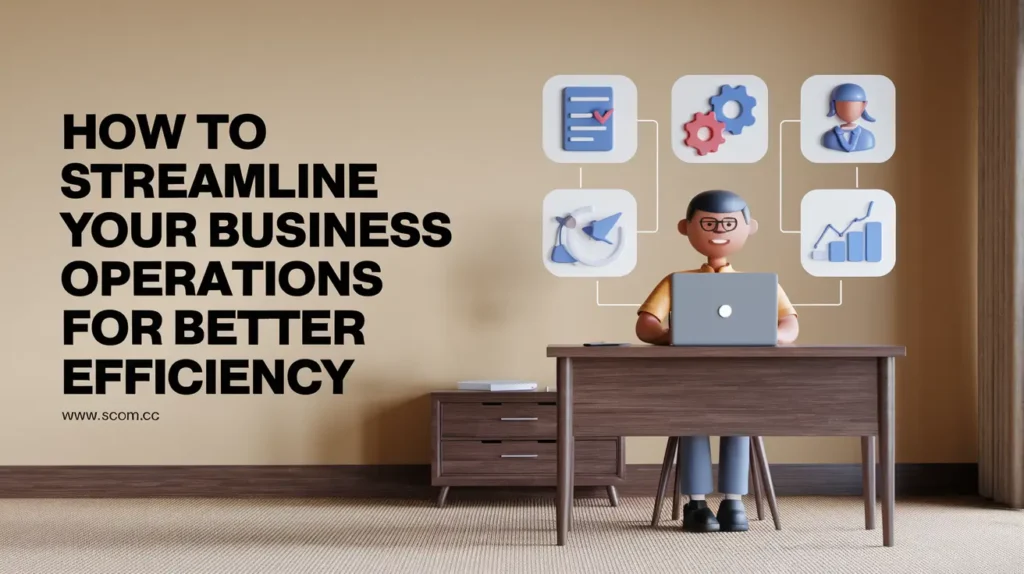
- How to Streamline Your Business Operations for Better Efficiency
- What Does Streamlining Business Operations Involve?
- How Can Technology Help in Streamlining Business Operations?
- What Are the Best Practices for Streamlining Business Processes?
- How Can Employee Training Contribute to Streamlining Operations?
- What Role Does Process Mapping Play in Streamlining Operations?
- How Can Standardisation Improve Efficiency in Business Operations?
- What Are the Key Metrics for Measuring Operational Efficiency?
- How Can Businesses Foster a Culture of Continuous Improvement?
- What Are Some Common Mistakes to Avoid When Streamlining Operations?
- How Can Businesses Measure the Success of Streamlining Initiatives?
-
FAQ
- What is process mapping and why is it important?
- How can technology improve business efficiency?
- What are some best practices for streamlining operations?
- How does employee training contribute to streamlined operations?
- What role does standardisation play in efficiency?
- What are key metrics for measuring operational efficiency?
- How can businesses foster a culture of continuous improvement?
How to Streamline Your Business Operations for Better Efficiency
What Does Streamlining Business Operations Involve?
Streamlining business operations involves optimising processes to enhance efficiency, reduce waste, and improve overall performance. This approach aims to make operations more effective and less resource-intensive. Here are the key components involved in streamlining business operations:
- Process Mapping: Begin by mapping out existing processes to identify inefficiencies, redundancies, and bottlenecks. Process mapping helps visualise workflows and understand how tasks flow from one stage to another.
- Workflow Analysis: Analyse workflows to determine which steps can be improved or eliminated. Focus on simplifying complex processes and reducing unnecessary steps to enhance productivity.
- Technology Integration: Incorporate technology solutions to automate repetitive tasks and improve accuracy. Technology can streamline communication, data management, and task execution, leading to increased efficiency.
- Standardisation: Standardise procedures and practices across the organisation to ensure consistency and reduce variation. Standardisation helps streamline training, improve quality, and simplify compliance.
- Employee Training: Provide training to employees on new processes, tools, and best practices. Well-trained staff are better equipped to handle streamlined processes and contribute to overall efficiency.
- Performance Metrics: Establish performance metrics to measure the effectiveness of streamlined processes. Metrics such as cycle time, error rates, and productivity levels provide insights into how well operations are performing.
- Continuous Improvement: Adopt a continuous improvement mindset by regularly reviewing and refining processes. Encourage feedback from employees and stakeholders to identify areas for further optimisation.
- Resource Allocation: Optimise resource allocation by ensuring that staff, materials, and equipment are used effectively. Efficient resource management reduces waste and maximises productivity.
- Customer Feedback: Incorporate customer feedback into process improvements. Understanding customer needs and preferences helps tailor operations to deliver better products and services.
- Change Management: Implement change management strategies to address resistance and ensure a smooth transition to streamlined processes. Effective change management supports employee buy-in and minimises disruption.
By focusing on these components, businesses can streamline their operations, leading to improved efficiency, reduced costs, and enhanced overall performance.
How Can Technology Help in Streamlining Business Operations?
Technology plays a crucial role in streamlining business operations by automating tasks, improving communication, and providing valuable data insights. Here’s how technology helps in this regard:
- Automation: Automation tools can handle repetitive and time-consuming tasks such as data entry, invoicing, and scheduling. By automating these tasks, businesses can reduce manual effort and minimise errors.
- Process Management Software: Process management software helps visualise and manage workflows, track progress, and identify bottlenecks. These tools enable businesses to optimise processes and improve efficiency.
- Cloud Computing: Cloud-based solutions provide access to data and applications from anywhere, facilitating collaboration and remote work. Cloud computing also offers scalability and flexibility for managing business operations.
- Data Analytics: Data analytics tools analyse performance metrics, customer behaviour, and market trends. These insights help businesses make informed decisions, identify areas for improvement, and optimise operations.
- Customer Relationship Management (CRM): CRM systems manage customer interactions, track sales, and analyse customer data. By improving customer relationship management, businesses can enhance customer satisfaction and streamline sales processes.
- Enterprise Resource Planning (ERP): ERP systems integrate various business functions such as finance, HR, and supply chain management. An ERP system provides a unified platform for managing operations and improving efficiency.
- Project Management Tools: Project management tools help plan, execute, and monitor projects. These tools facilitate collaboration, track project progress, and ensure that projects are completed on time and within budget.
- Communication Tools: Modern communication tools, such as instant messaging, video conferencing, and collaboration platforms, enhance internal communication and streamline information sharing among teams.
- Supply Chain Management Software: Supply chain management software optimises inventory management, order processing, and supplier relationships. Efficient supply chain management reduces delays and improves operational efficiency.
- Business Intelligence (BI) Tools: BI tools provide visualisations, dashboards, and reports that help businesses monitor performance and make data-driven decisions. BI tools support strategic planning and operational improvements.
By leveraging these technological solutions, businesses can streamline operations, enhance productivity, and achieve better overall efficiency.
What Are the Best Practices for Streamlining Business Processes?
Implementing best practices for streamlining business processes involves focusing on key strategies and methodologies that enhance efficiency and effectiveness. Here are some best practices:
- Document Processes: Clearly document all business processes to create a reference for employees and stakeholders. Documentation helps ensure consistency and serves as a basis for identifying areas for improvement.
- Identify Key Processes: Focus on identifying and streamlining key processes that have the most significant impact on business performance. Prioritising these processes can yield the greatest benefits in terms of efficiency and effectiveness.
- Eliminate Redundancies: Review processes to identify and eliminate redundant steps and activities. Streamlining workflows by removing unnecessary tasks helps reduce complexity and improve overall efficiency.
- Leverage Automation: Implement automation tools to handle repetitive tasks and improve accuracy. Automation reduces manual effort and frees up time for employees to focus on higher-value activities.
- Standardise Procedures: Develop and implement standard operating procedures (SOPs) to ensure consistency in how tasks are performed. Standardisation simplifies training, improves quality, and enhances efficiency.
- Monitor Performance: Regularly monitor performance metrics and key performance indicators (KPIs) to assess the effectiveness of streamlined processes. Use data to identify areas for further improvement and make necessary adjustments.
- Foster Collaboration: Encourage collaboration and communication among teams to streamline information flow and decision-making. Collaborative efforts help ensure that all team members are aligned and working towards common goals.
- Engage Employees: Involve employees in the process of streamlining operations by seeking their feedback and insights. Employee engagement helps identify practical improvements and fosters a culture of continuous improvement.
- Invest in Training: Provide training and support to employees on new processes, tools, and best practices. Well-trained staff are better equipped to adapt to streamlined processes and contribute to overall efficiency.
- Regularly Review and Optimise: Continuously review and optimise processes to ensure they remain effective and efficient. Regular reviews help identify emerging issues and opportunities for further improvements.
By following these best practices, businesses can effectively streamline their processes, enhance efficiency, and achieve better operational performance.
How Can Employee Training Contribute to Streamlining Operations?
Employee training is a critical component of streamlining operations as it equips staff with the skills and knowledge needed to effectively implement and manage streamlined processes. Here’s how employee training contributes to operational efficiency:
- Skill Development: Training enhances employees' skills and competencies, enabling them to perform tasks more efficiently and accurately. Skilled employees can adapt to new processes and technologies, leading to improved overall efficiency.
- Process Understanding: Training helps employees understand new or revised processes, procedures, and workflows. A clear understanding of how tasks fit into the broader operational framework ensures that processes are followed correctly.
- Increased Productivity: Well-trained employees work more efficiently and make fewer errors, resulting in increased productivity. Training helps staff become proficient in using new tools and technologies that streamline operations.
- Consistency: Training ensures that employees follow standard procedures and best practices consistently. Consistent execution of tasks and processes reduces variation and enhances overall operational efficiency.
- Change Management: Training supports change management efforts by helping employees adapt to new processes and systems. Effective training reduces resistance to change and facilitates a smoother transition to streamlined operations.
- Enhanced Problem-Solving: Training improves employees' problem-solving skills, enabling them to address issues and challenges more effectively. Well-trained staff can quickly identify and resolve problems that may arise during streamlined processes.
- Better Communication: Training enhances communication skills, leading to more effective collaboration and information sharing among team members. Improved communication supports streamlined workflows and reduces misunderstandings.
- Knowledge Retention: Ongoing training helps retain knowledge and skills within the organisation. Knowledgeable employees contribute to the maintenance and continuous improvement of streamlined processes.
- Employee Engagement: Investing in training demonstrates a commitment to employee development, which can boost morale and engagement. Engaged employees are more motivated to contribute to operational efficiency and process improvements.
- Compliance and Quality: Training ensures that employees are aware of and adhere to compliance requirements and quality standards. Adherence to these standards is crucial for maintaining streamlined and efficient operations.
Overall, employee training is essential for streamlining operations as it equips staff with the necessary skills, knowledge, and tools to implement and manage efficient processes effectively.
What Role Does Process Mapping Play in Streamlining Operations?
Process mapping is a vital tool in streamlining operations as it provides a visual representation of workflows, tasks, and interactions. Here’s how process mapping contributes to operational efficiency:
- Visualisation: Process mapping visualises the flow of tasks and activities, making it easier to understand how processes function and interact. Visual representations help identify inefficiencies, redundancies, and bottlenecks.
- Identification of Inefficiencies: By mapping out processes, businesses can pinpoint areas where inefficiencies occur, such as delays, duplicate efforts, or unnecessary steps. Identifying these inefficiencies allows for targeted improvements.
- Standardisation: Process mapping helps standardise procedures by providing a clear and consistent reference for how tasks should be performed. Standardisation ensures that processes are executed uniformly across the organisation.
- Improved Communication: Process maps facilitate communication among team members by providing a common understanding of workflows and responsibilities. Clear communication helps align efforts and streamline operations.
- Training and Onboarding: Process maps serve as valuable training and onboarding tools for new employees. They provide a visual guide to understanding workflows and responsibilities, speeding up the learning process.
- Documentation: Process mapping creates a documented record of how processes are executed. This documentation serves as a reference for future improvements and ensures continuity in case of staff changes.
- Change Management: When implementing changes to processes, process maps help illustrate how new procedures will be integrated into existing workflows. This clarity supports smoother transitions and reduces resistance.
- Continuous Improvement: Process mapping supports continuous improvement efforts by providing a basis for analysing and refining processes. Regularly updated process maps help track changes and measure their impact on efficiency.
- Decision-Making: Process maps provide insights that aid decision-making by highlighting areas that require attention or improvement. Data-driven decisions can be made based on a clear understanding of process performance.
- Compliance: Process maps help ensure compliance with regulations and standards by clearly outlining procedures and controls. They provide a basis for audits and assessments to verify adherence to requirements.
In summary, process mapping is a crucial tool for streamlining operations as it helps visualise, analyse, and improve workflows, leading to enhanced efficiency and effectiveness.
How Can Standardisation Improve Efficiency in Business Operations?
Standardisation involves creating uniform procedures and practices across an organisation to ensure consistency and efficiency. Here’s how standardisation improves efficiency in business operations:
- Consistency: Standardisation ensures that tasks and processes are performed consistently, reducing variation and errors. Consistent practices lead to predictable outcomes and improved quality.
- Simplified Training: With standardised procedures, training becomes more straightforward and efficient. Employees learn a consistent approach, which reduces the time and resources needed for training.
- Improved Communication: Standardisation fosters clear and effective communication by providing a common framework for how tasks should be executed. This clarity reduces misunderstandings and enhances collaboration.
- Increased Productivity: Standardised processes streamline workflows and reduce the time spent on decision-making and problem-solving. Employees can focus on their tasks without needing to navigate different procedures.
- Easier Compliance: Standardisation helps ensure compliance with regulations and industry standards by providing a consistent approach to meeting requirements. Compliance becomes more manageable with uniform procedures.
- Enhanced Quality Control: Standardised procedures make it easier to monitor and control quality. Consistent practices enable better quality assurance and reduce the likelihood of defects or errors.
- Efficient Resource Utilisation: Standardisation helps optimise resource allocation by providing clear guidelines on how resources should be used. This reduces waste and ensures that resources are deployed effectively.
- Streamlined Processes: Standardisation eliminates unnecessary steps and redundancies, resulting in more efficient processes. Streamlined workflows lead to faster execution and reduced operational costs.
- Better Performance Measurement: Standardised processes provide a basis for measuring performance and identifying areas for improvement. Metrics and KPIs can be more accurately assessed when processes are uniform.
- Scalability: Standardisation facilitates scalability by providing a replicable model for expanding operations. As the business grows, standardised processes can be easily scaled to accommodate increased demands.
By implementing standardisation, businesses can enhance efficiency, reduce costs, and improve overall operational performance.
What Are the Key Metrics for Measuring Operational Efficiency?
Measuring operational efficiency involves tracking various metrics that provide insights into how well processes are performing. Here are some key metrics for evaluating operational efficiency:
- Cycle Time: Cycle time measures the total time taken to complete a specific process or task from start to finish. Shorter cycle times indicate higher efficiency and faster execution.
- Throughput: Throughput refers to the amount of work or number of units processed within a given time period. Higher throughput indicates increased productivity and efficiency.
- Error Rate: Error rate measures the frequency of errors or defects in processes or outputs. A lower error rate signifies higher accuracy and better operational efficiency.
- Utilisation Rate: Utilisation rate measures the extent to which resources, such as equipment or personnel, are used effectively. Higher utilisation rates indicate better resource management and efficiency.
- Cost per Unit: Cost per unit calculates the cost incurred to produce a single unit of output. Lower costs per unit reflect improved cost efficiency and effective resource management.
- Customer Satisfaction: Customer satisfaction metrics assess how well products or services meet customer expectations. Higher satisfaction levels indicate that operations are effectively meeting customer needs.
- Lead Time: Lead time measures the time taken to fulfill a customer order or complete a task from the moment it is initiated. Shorter lead times reflect improved operational efficiency and responsiveness.
- Inventory Turnover: Inventory turnover measures how quickly inventory is sold and replaced within a specific period. Higher turnover rates indicate efficient inventory management and reduced holding costs.
- Employee Productivity: Employee productivity metrics evaluate the output or performance of employees relative to the resources invested. Higher productivity levels reflect efficient use of human resources.
- Return on Investment (ROI): ROI measures the financial return generated from investments in operational improvements. A higher ROI indicates that investments in streamlining operations are yielding positive results.
By monitoring these key metrics, businesses can gain valuable insights into their operational efficiency and identify areas for improvement.
How Can Businesses Foster a Culture of Continuous Improvement?
Fostering a culture of continuous improvement involves creating an environment where employees are encouraged to seek out and implement enhancements to processes and practices. Here’s how businesses can promote this culture:
- Encourage Innovation: Promote an innovative mindset by encouraging employees to propose and experiment with new ideas. Recognise and reward creativity and problem-solving efforts.
- Provide Training and Development: Offer ongoing training and development opportunities to enhance employees’ skills and knowledge. Continuous learning supports the implementation of new practices and technologies.
- Set Clear Goals: Establish clear and measurable goals for continuous improvement initiatives. Ensure that employees understand the objectives and how their efforts contribute to achieving them.
- Foster Open Communication: Create an open communication environment where employees feel comfortable sharing their ideas and feedback. Regularly solicit input and suggestions for process improvements.
- Implement Feedback Mechanisms: Develop mechanisms for collecting and acting on feedback from employees, customers, and stakeholders. Use feedback to identify areas for improvement and make necessary changes.
- Encourage Collaboration: Promote collaboration and teamwork to leverage diverse perspectives and expertise. Collaborative efforts can lead to more effective problem-solving and process improvements.
- Recognise and Reward Achievements: Acknowledge and reward employees for their contributions to continuous improvement. Recognition and rewards motivate employees to actively engage in improvement efforts.
- Support Experimentation: Encourage employees to experiment with new approaches and solutions. Provide resources and support for testing and evaluating new ideas to drive continuous improvement.
- Monitor Progress: Regularly monitor progress towards improvement goals and track the impact of implemented changes. Use performance metrics to evaluate the effectiveness of continuous improvement efforts.
- Lead by Example: Demonstrate a commitment to continuous improvement at all levels of the organisation. Leadership support and involvement are crucial for fostering a culture of ongoing enhancement.
By promoting a culture of continuous improvement, businesses can drive ongoing enhancements to processes, increase efficiency, and achieve better overall performance.
What Are Some Common Mistakes to Avoid When Streamlining Operations?
When streamlining operations, businesses should be aware of common mistakes that can hinder efficiency and effectiveness. Here are some mistakes to avoid:
- Neglecting Process Mapping: Failing to map out existing processes can lead to overlooking inefficiencies and bottlenecks. Process mapping is essential for identifying areas for improvement and developing effective solutions.
- Ignoring Employee Feedback: Disregarding feedback from employees can result in missed opportunities for improvement and resistance to change. Involve employees in the process and consider their insights.
- Overlooking Training Needs: Insufficient training can lead to poor implementation of new processes and tools. Ensure that employees receive adequate training to adapt to changes effectively.
- Implementing Too Many Changes at Once: Introducing multiple changes simultaneously can overwhelm employees and disrupt operations. Prioritise and implement changes gradually to minimise disruption.
- Failing to Monitor Performance: Not monitoring performance metrics can prevent businesses from identifying issues and measuring the impact of improvements. Regularly track performance to ensure that changes are effective.
- Neglecting Change Management: Ignoring change management strategies can lead to resistance and hinder the successful implementation of new processes. Address resistance and support employees through transitions.
- Inadequate Resource Allocation: Poor resource allocation can undermine the effectiveness of streamlined processes. Ensure that resources are allocated efficiently to support new processes and technologies.
- Not Setting Clear Objectives: Lack of clear objectives can lead to unfocused efforts and suboptimal results. Define clear goals for streamlining initiatives to guide efforts and measure success.
- Failing to Involve Stakeholders: Not involving key stakeholders in the process can result in misalignment and lack of support. Engage stakeholders to ensure that their needs and perspectives are considered.
- Ignoring Continuous Improvement: Treating streamlining as a one-time effort rather than an ongoing process can limit long-term benefits. Adopt a continuous improvement mindset to drive ongoing enhancements.
By avoiding these common mistakes, businesses can improve their approach to streamlining operations and achieve better efficiency and effectiveness.
How Can Businesses Measure the Success of Streamlining Initiatives?
Measuring the success of streamlining initiatives involves evaluating the impact of changes on various aspects of operations. Here’s how businesses can measure success:
- Evaluate Performance Metrics: Assess performance metrics and KPIs related to the streamlined processes. Metrics such as cycle time, throughput, and error rates provide insights into the effectiveness of changes.
- Monitor Cost Savings: Calculate cost savings achieved through streamlining initiatives. Compare costs before and after implementing changes to determine the financial impact of improvements.
- Assess Productivity Improvements: Measure improvements in productivity resulting from streamlined processes. Increased output or reduced time per task indicates successful efficiency enhancements.
- Gather Employee Feedback: Collect feedback from employees on their experiences with the new processes. Positive feedback and increased satisfaction suggest that the changes are effective.
- Review Customer Satisfaction: Evaluate customer satisfaction levels to determine if streamlined processes have led to better service or product quality. Higher satisfaction indicates successful improvements.
- Track Compliance: Verify that the streamlined processes meet compliance requirements and industry standards. Successful compliance reflects the effectiveness of changes in maintaining standards.
- Analyse Return on Investment (ROI): Calculate the ROI of streamlining initiatives by comparing the benefits achieved against the costs incurred. A positive ROI indicates that the changes are yielding valuable results.
- Monitor Lead Time: Assess changes in lead time for completing tasks or fulfilling orders. Reduced lead times indicate improved efficiency and effectiveness of streamlined processes.
- Review Resource Utilisation: Evaluate changes in resource utilisation to ensure that resources are used effectively and efficiently. Improved resource management reflects successful streamlining.
- Conduct Post-Implementation Reviews: Perform post-implementation reviews to assess the overall impact of streamlining initiatives. Review results against objectives and identify areas for further improvement.
By using these methods to measure success, businesses can determine the effectiveness of their streamlining initiatives and make data-driven decisions for future improvements.
Summary Table
Aspect | Key Points |
---|---|
Streamlining Involves | Process mapping, workflow analysis, technology integration, standardisation, employee training, performance metrics, continuous improvement, resource allocation, customer feedback, change management |
Technology Benefits | Automation, process management software, cloud computing, data analytics, CRM, ERP, project management tools, communication tools, supply chain management software, BI tools |
Best Practices | Document processes, identify key processes, eliminate redundancies, leverage automation, standardise procedures, monitor performance, foster collaboration, engage employees, invest in training, regularly review and optimise |
Employee Training Impact | Skill development, process understanding, increased productivity, consistency, change management, enhanced problem-solving, better communication, knowledge retention, employee engagement, compliance and quality |
Process Mapping Role | Visualisation, identification of inefficiencies, standardisation, improved communication, training and onboarding, documentation, change management, continuous improvement, decision-making, compliance |
Standardisation Benefits | Consistency, simplified training, improved communication, increased productivity, easier compliance, enhanced quality control, efficient resource utilisation, streamlined processes, better performance measurement, scalability |
Key Metrics | Cycle time, throughput, error rate, utilisation rate, cost per unit, customer satisfaction, lead time, inventory turnover, employee productivity, ROI |
Culture of Continuous Improvement | Encourage innovation, provide training, set clear goals, foster open communication, implement feedback mechanisms, encourage collaboration, recognise achievements, support experimentation, monitor progress, lead by example |
Common Mistakes | Neglecting process mapping, ignoring employee feedback, overlooking training needs, implementing too many changes, failing to monitor performance, neglecting change management, inadequate resource allocation, not setting clear objectives, failing to involve stakeholders, ignoring continuous improvement |
Measuring Success | Evaluate performance metrics, monitor cost savings, assess productivity improvements, gather employee feedback, review customer satisfaction, track compliance, analyse ROI, monitor lead time, review resource utilisation, conduct post-implementation reviews |
FAQ
What is process mapping and why is it important?
Process mapping involves creating a visual representation of workflows and processes to understand how tasks flow and identify inefficiencies. It is important because it helps businesses pinpoint areas for improvement, streamline operations, and enhance overall efficiency.
How can technology improve business efficiency?
Technology can improve business efficiency by automating repetitive tasks, integrating various functions through software, providing data analytics for informed decision-making, and facilitating better communication and collaboration.
What are some best practices for streamlining operations?
Best practices include documenting processes, identifying key areas for improvement, leveraging automation, standardising procedures, monitoring performance metrics, and engaging employees in the improvement process.
How does employee training contribute to streamlined operations?
Employee training ensures that staff are skilled and knowledgeable about new processes and tools, leading to increased productivity, consistency, and effective implementation of streamlined operations.
What role does standardisation play in efficiency?
Standardisation ensures that processes are performed consistently, simplifies training, improves communication, and enhances quality control, all of which contribute to greater operational efficiency.
What are key metrics for measuring operational efficiency?
Key metrics include cycle time, throughput, error rate, utilisation rate, cost per unit, customer satisfaction, lead time, inventory turnover, employee productivity, and return on investment (ROI).
How can businesses foster a culture of continuous improvement?
Businesses can foster a culture of continuous improvement by encouraging innovation, providing ongoing training, setting clear goals, fostering open communication, recognising achievements, and supporting experimentation and feedback.
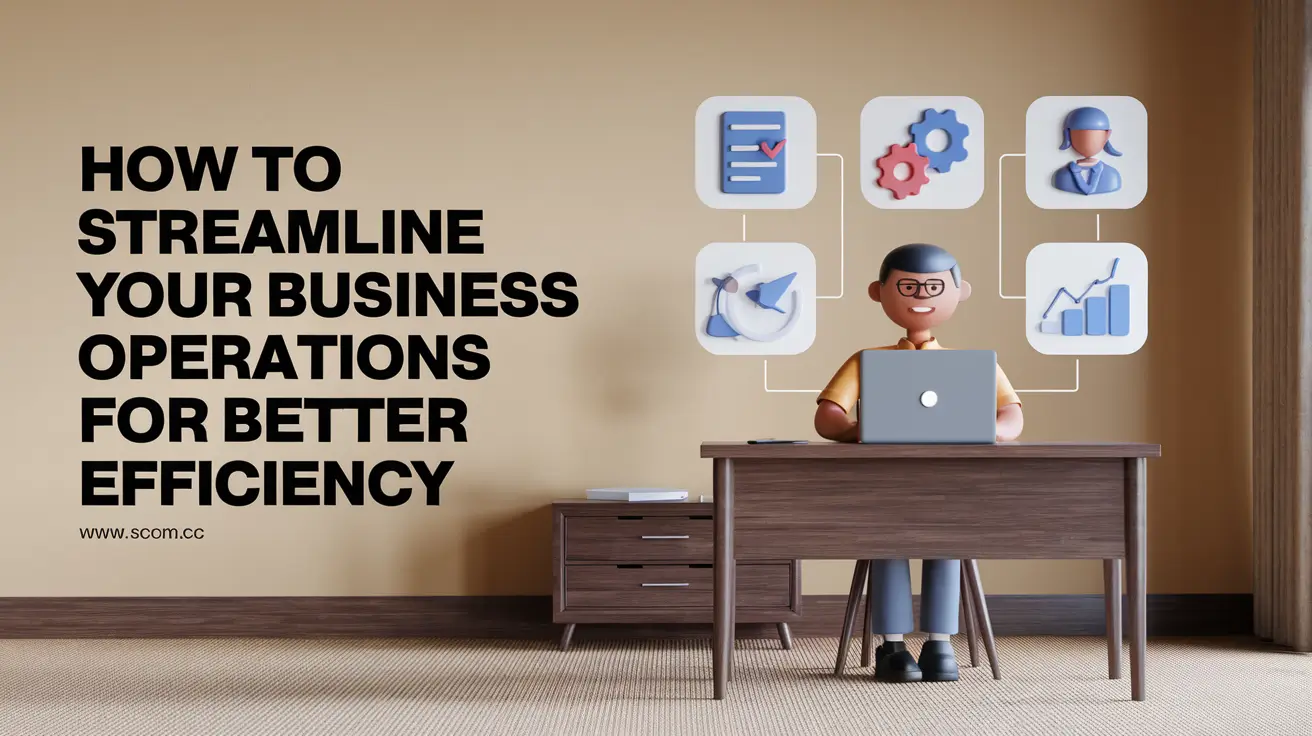
If you enjoyed this article and found it valuable, we encourage you to explore our news and valuable information section, where you'll find more relevant and up-to-date content that may pique your interest. Additionally, if you are seeking advice or need guidance on a specific topic, we suggest visiting our services section. There, you will find a variety of options designed to assist and support you in addressing your needs. Feel free to check out both sections to get the information and assistance that best suits your requirements.
Leave a Reply